Blog
Three trends defining logistics today: How to leverage and drive value
Richard Cawston, Chief Revenue Officer, President of Europe
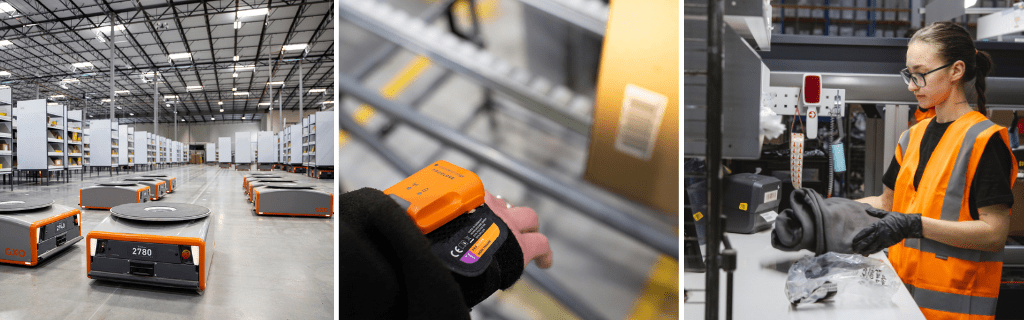
The world economy has been on a rollercoaster ride the last few years, with the pandemic significantly shifting the way in which supply chains performed and consumers behave. It also revealed areas where change is needed. Now, there is an increasing realization that those changes are not temporary and global companies are actively evolving their operations to navigate a more uncertain world.
As I talk to our teams and our customers around the world, I see three main trends driving growth and change in the industry.
Cost efficiencies are high on the agenda
2024 started off with a bang, between the impact of geopolitical disruptions, ongoing shifts in the global economic order, the need for energy transition and the appearance of new technology platforms. Most of all, worries about the economy persist.
According to a recent McKinsey report, uncertainty about economic growth – the GDP growth estimate for China is 3%, 1% for the US, and 0.8% for Europe – is leading companies to cut costs across the board to achieve growth and profitability.
Significant opportunities exist for companies to mitigate cost inflation through optimizing logistics.
Achieving cost-savings in logistics requires strategic thinking, proactive measures and technology. Ineffective warehouses, minor process inefficiencies, and inventory allocation mishaps have a considerable effect on supply chains and lead to increased costs for consumers. Addressing this requires a combination of actions such as deploying automation, upskilling workers, sharing warehouses, and limiting overstocks.
As we partner with customers, we hear a clear call for solutions that free up resources, reduce costs, and maximize flexibility. We’re also hearing a need for speed, while still maintaining capacity for long-term growth. Outsourcing logistics to a world-class provider can raise service levels; increase employee safety, productivity, and engagement; and materially improve business results.
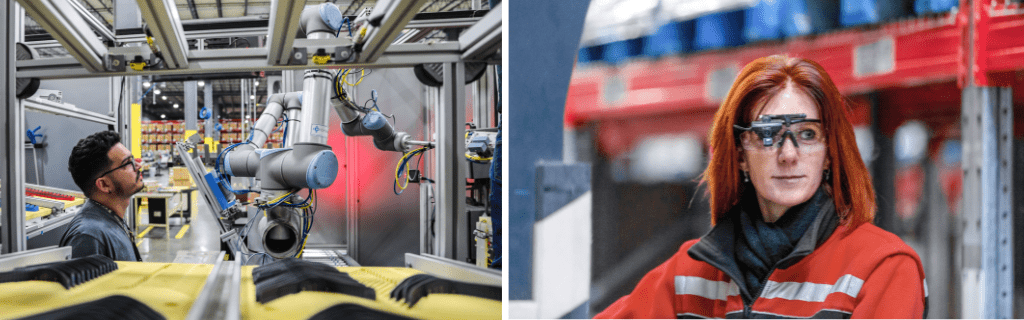
Labor cost and availability remain persistent challenges
In our post-pandemic world, a new type of workforce has emerged. Surveys have shown that 40% of workers globally might leave their jobs in the near future, citing a lack of flexibility, support for health and well-being, and meaningful work.
The increase in temporary workers and volume of turnover has only risen and will continue to do so. Between 2020 and 2022, 55% of workers in the travel, transportation, and logistics industries moved to a different industry.
All of these factors have contributed to significantly higher labor costs and higher attrition.
Investing in higher quality work environments, where employees can develop their skills and be trained to use cutting-edge technology, will help mitigate this issue and ensure employees are not left behind in the logistics industry of the future. As an industry, we should aim to create workplaces where automation and technology work in service of employees to eliminate health hazards and risks, and to reduce menial work so they have capacity to perform higher-acuity tasks. In addition to utilizing automated hardware solutions, the industry is also actively trialing and deploying AI technologies that can produce significant benefits in areas such as accuracy and efficiency.
Taking these steps should reduce turnover and empower people to provide greater value.
Avoiding waste and moving towards a circular economy unlocks value
There has been much discussion in recent months about the perceived value of ESG commitments. However, this debate over increasing norms and competing standards may have obscured the fact that companies and consumers across industries are steadily moving towards a circular economy in which options for returns, repairs and refurbishments are becoming the industry standard and increasingly mandated by legislation.
There is considerable value in this secondary market, and manufacturers and retailers need to invest in efficient return and repair solutions to stay ahead of the game. The benefits of this investment can be game changing: we’ve seen examples of customers able to repair and resell more than 95% of returned items, reducing the volume of waste sent to landfills and materially improving margins. The bottom line is, when we can make our resources go further, everyone does better.
I’m very proud of how comprehensive GXO’s reverse logistics has become. Yet even though we’re now able to manage the entire returns process, including inbound receipt, inspection, refurbishment, repackaging, and return-to-retail or disposal, as well as refund management and warranty claims adjudication, we must continue look for ways to extend this sustainable mindset to other parts of the business, so it becomes the norm in every aspect of our supply chain, and for every partner with whom we engage.